Plastic Injection Molding Manufacturing: A Comprehensive Guide
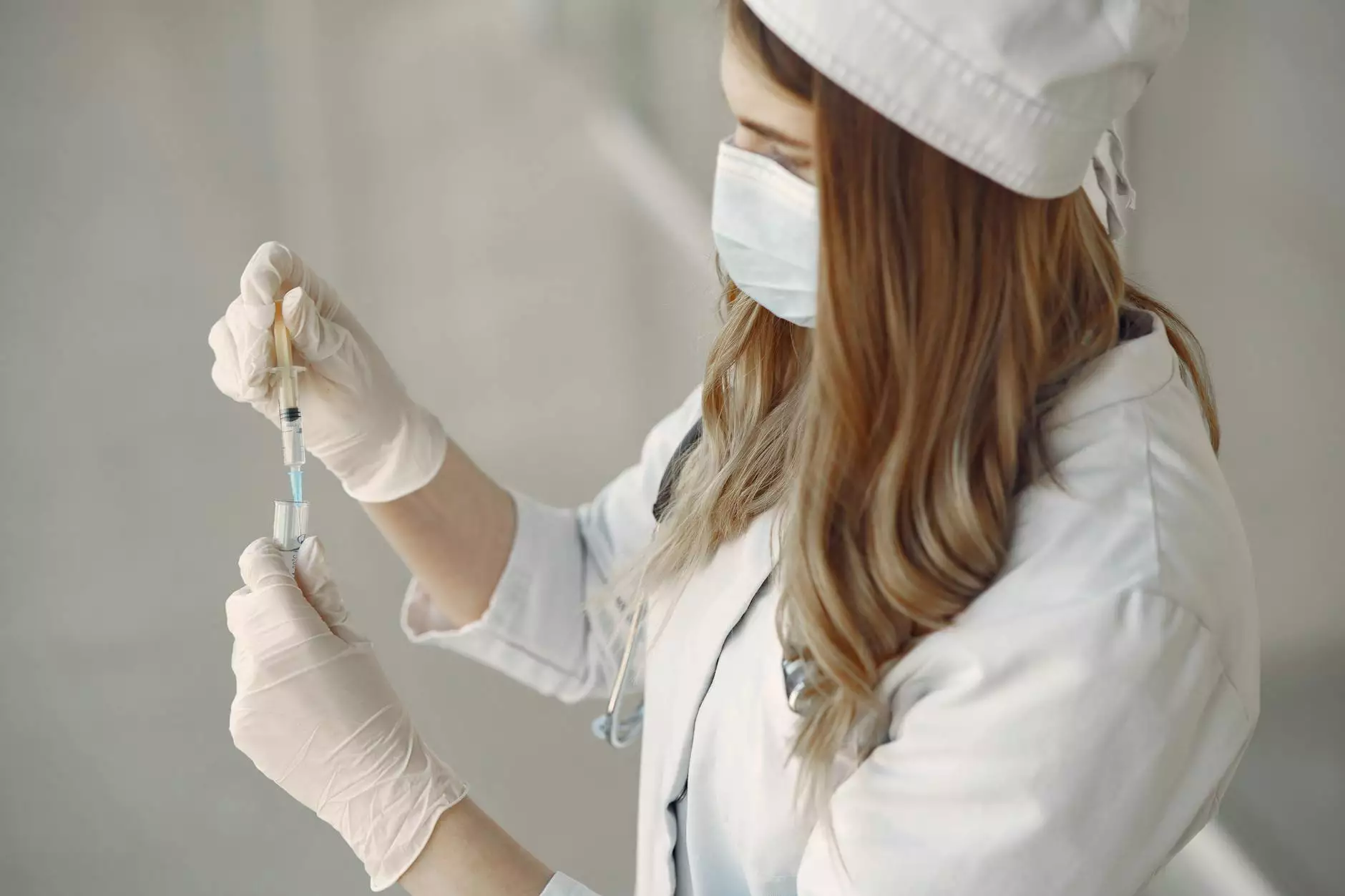
In the fast-evolving world of manufacturing, plastic injection molding stands out as a pivotal process that has radically transformed the way products are fabricated. This innovative technique offers unparalleled precision, efficiency, and versatility, making it a preferred choice for numerous industries, including automotive, consumer goods, and medical sectors. The following sections delve deep into the nuances of plastic injection molding manufacturing, exploring its mechanisms, benefits, and its critical role within the broader manufacturing landscape.
What is Plastic Injection Molding?
Plastic injection molding is a manufacturing process used to produce parts by injecting molten plastic into a mold. The technique involves several key steps:
- Melting: Plastic pellets are fed into a heated barrel, where they are melted into a molten resin.
- Injection: The molten plastic is injected into a mold under high pressure.
- Cooling: The injected plastic cools and solidifies within the mold.
- Ejection: Once cooled, the mold is opened and the finished part is ejected.
The History of Plastic Injection Molding
The roots of plastic injection molding can be traced back to the early 19th century, creating a fascinating story of innovation. The original method involved hand-operated machinery, but as technology advanced, the process became more efficient and automated. The invention of the screw injection molding machine in the 1950s marked a significant turning point, allowing for increased speed and consistency in production. Today, the industry utilizes computer numerical control (CNC) and advanced robotics to optimize manufacturing processes.
Benefits of Plastic Injection Molding Manufacturing
The advantages of plastic injection molding manufacturing are numerous and impactful:
- High Efficiency: Injection molding is known for its speed, producing thousands of identical parts in a single production run.
- Design Flexibility: Manufacturers can create complex shapes and detailed designs that would be impossible with traditional manufacturing methods.
- Reduced Waste: The process generates minimal waste compared to other methods, contributing to sustainability efforts.
- Cost-Effective for Large Volumes: While the initial setup costs can be high, the per-unit cost decreases significantly with mass production.
- Material Variety: Various materials, including thermoplastics and thermosets, can be used, providing manufacturers with numerous options for product performance.
Applications of Plastic Injection Molding in Various Industries
Plastic injection molding manufacturing finds applications across numerous sectors. Here’s a closer look at some industries benefiting from this exceptional process:
1. Automotive Industry
In the automotive sector, precision and durability are paramount. Plastic injection molding is widely used to manufacture components such as dashboards, bumpers, and switches. The process allows for intricate designs that meet stringent safety and performance standards.
2. Consumer Goods
From toys to kitchen appliances, the consumer goods sector relies heavily on plastic injection molding for its rapid production capabilities and ability to create various shapes and colors, enabling brands to deliver attractive products efficiently.
3. Medical Devices
In the medical field, where cleanliness and precision are critical, plastic injection molding manufacturing ensures the production of sterile and accurate components such as syringes, surgical tools, and diagnostic devices. The process meets strict regulatory requirements, ensuring patient safety.
4. Electronics
Plastic components are integral to electronic devices. Plastic injection molding is utilized for manufacturing enclosures, connectors, and other parts, facilitating mass production and ensuring product reliability.
The Process of Plastic Injection Molding: A Detailed Examination
Understanding the steps involved in plastic injection molding manufacturing can provide insights into its complexities:
1. Material Preparation
The process begins with the selection of appropriate raw material, typically in pellet form. The pellets are carefully chosen based on the desired properties of the final product, such as flexibility, strength, and temperature resistance.
2. Melting and Injection
The pellets are then heated until they melt into a viscous state. A reciprocating screw mechanism injects this molten plastic into the mold cavity with precision and speed, ensuring a consistent flow that fills every detail of the mold.
3. Cooling and Solidification
Upon injection, the hot plastic begins to cool and solidify, taking the shape of the mold. Cooling channels within the mold help to control the temperature and speed up this process, reducing cycle times and improving efficiency.
4. Ejection
Once the plastic has cooled sufficiently, the mold opens, and ejector pins push the finished part out. This stage requires careful handling to avoid damaging the newly formed product.
Challenges in Plastic Injection Molding Manufacturing
Despite its many advantages, plastic injection molding manufacturing also faces several challenges:
- High Initial Costs: Setting up molds can be expensive, which is a significant barrier for small production runs.
- Complexity in Design Changes: Once a mold is created, modifications can be costly and time-consuming.
- Material Limitations: Not all plastics are suitable for injection molding, which can restrict the selection of materials.
Future Trends in Plastic Injection Molding Manufacturing
The future of plastic injection molding is promising, with advancements in technology paving the way for enhanced processes:
1. Smart Manufacturing
The integration of IoT and smart manufacturing technologies is expected to enhance operational efficiency. Real-time data collection will help monitor machine performance and reduce downtime.
2. Sustainable Practices
As industries move towards sustainability, the use of biodegradable plastics and recycled materials in plastic injection molding is on the rise, aiming to reduce the environmental impact of production.
3. Increased Automation
Automation through robotics will streamline processes further, increasing production rates and improving precision, thereby allowing manufacturers to meet the growing demands efficiently.
Conclusion
In conclusion, plastic injection molding manufacturing is an essential and versatile process that has become integral to modern manufacturing. Its efficiency, cost-effectiveness, and ability to produce complex shapes make it an invaluable asset across various industries. As technology continues to advance, the process is set to evolve, promising even greater efficiencies and innovations. Companies wishing to thrive in today’s competitive markets must embrace the potential of plastic injection molding and harness its capabilities to drive growth and sustainability.
Contact DeepMould for Your Injection Molding Needs!
If you're interested in leveraging the benefits of plastic injection molding manufacturing for your business, contact DeepMould at deepmould.net. Our expertise in metal fabricators and commitment to quality will help bring your ideas to life with precision and excellence!