Trade for Automotive Injection Molding: Revolutionizing the Industry
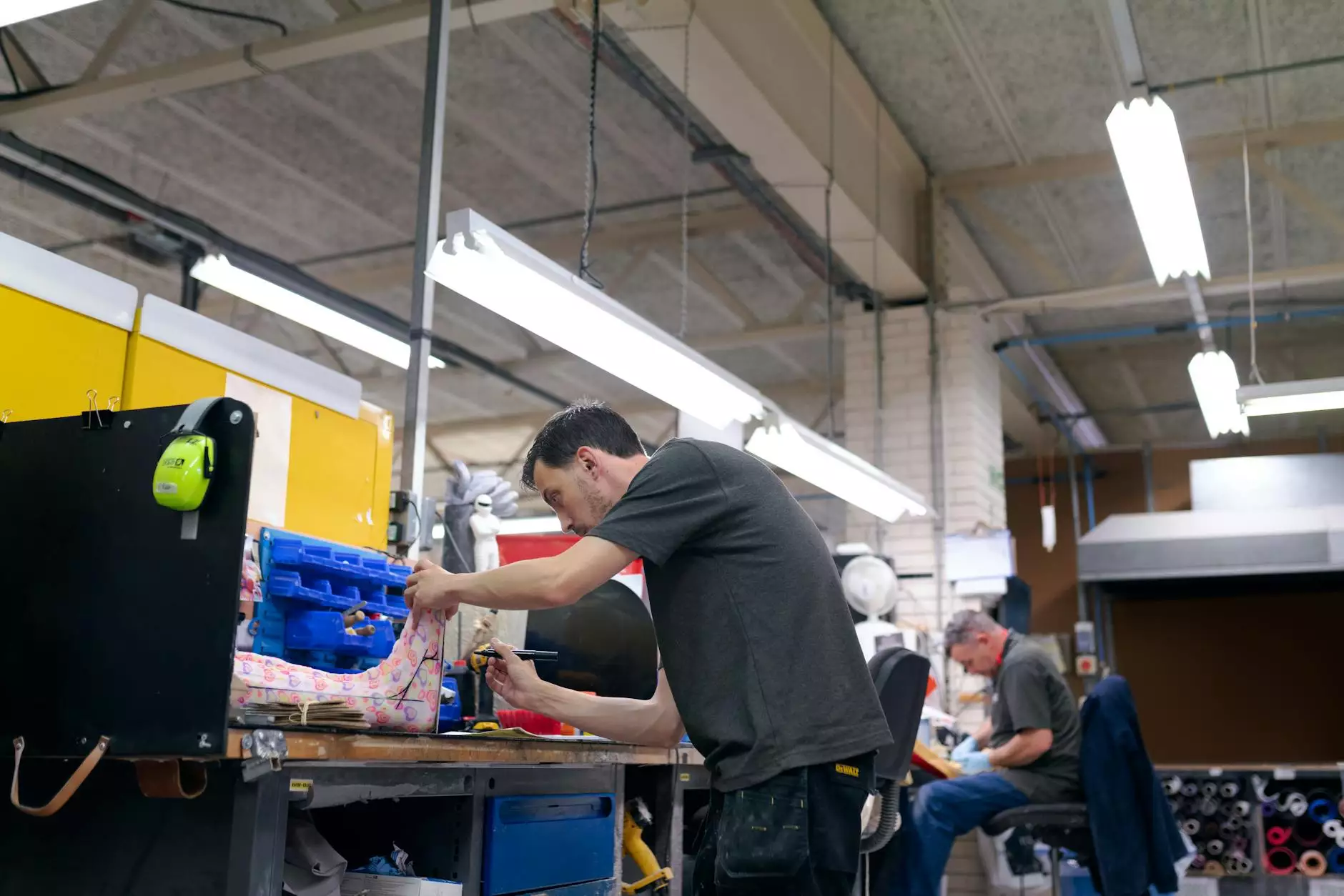
The automotive industry has undergone remarkable transformations over the past few decades, largely thanks to advancements in manufacturing technology. Among these advancements, automotive injection molding stands out as a key innovation that has immensely improved production efficiency and design flexibility. In this article, we dive deep into the realm of trade for automotive injection molding, exploring its benefits, applications, and future trends.
Understanding Automotive Injection Molding
Automotive injection molding is a manufacturing process where molten materials, typically plastics, are injected into a mold to create components for vehicles. This method allows for high-volume production and precision, making it ideal for the automotive sector where consistency and quality are paramount.
The Process of Injection Molding
The injection molding process consists of several crucial steps:
- Material Selection: The process begins with the selection of the appropriate plastic material, which can range from thermoplastics to thermosetting plastics.
- Mold Design: A mold is designed based on the component specifications. The mold is typically made of metal, ensuring durability and precision.
- Injection: Once the mold is prepared, the plastic material is heated until it becomes molten and then injected into the mold under high pressure.
- Cooling: After injection, the molten plastic cools and solidifies inside the mold, taking on its final shape.
- De-molding: Once cooled, the mold is opened, and the finished part is ejected. This process can be repeated multiple times to produce large quantities of components efficiently.
Why Trade for Automotive Injection Molding is Essential
As the demand for automotive components continues to grow, the trade for automotive injection molding offers significant advantages over traditional manufacturing techniques. These benefits include:
- Cost Efficiency: Injection molding minimizes waste of materials and optimizes production processes, reducing overall costs.
- High Precision: The use of molds allows for a high degree of precision and repeatability in manufacturing, ensuring each part meets stringent industry standards.
- Complex Designs: Injection molding techniques enable manufacturers to create intricate designs that would be challenging or impossible with other methods.
- Material Versatility: There is a wide range of materials available for injection molding, including advanced polymers that meet the demanding requirements of the automotive sector.
Applications in the Automotive Industry
Injection molded parts are integral to many automotive components. Some common applications include:
Interior Components
Injection molding is widely used to create interior components such as:
- Dashboard elements: Complex shapes and features can be produced for improved aesthetics and ergonomics.
- Door panels: Lightweight and durable panels that contribute to vehicle structure.
- Seating components: Molded parts that enhance comfort and style.
Exterior Components
When it comes to exterior parts, injection molding plays a vital role in the creation of:
- Bumpers: Designed for impact resistance while maintaining a stylish appearance.
- Body panels: Lightweight designs that improve fuel efficiency without compromising safety.
- Lighting housings: Precise molds that ensure fit and function of automotive lighting.
Functional Components
Functional components of vehicles that benefit from injection molding include:
- Engine covers: Protect vital components while enhancing aesthetics.
- Housings for sensors and electronics: Vital for modern automotive technology integration.
- Fluid reservoirs: Engineered for durability in challenging environments.
The Future of Automotive Injection Molding
The future of trade for automotive injection molding looks promising as technological advances continue to drive the industry forward. Innovations such as:
- 3D Printing Integration: The use of 3D printing for mold design and prototyping significantly speeds up the development process.
- Biodegradable Plastics: Environmentally friendly materials that reduce the carbon footprint of automotive manufacturing.
- Smart Manufacturing: Implementing IoT and automation in injection molding processes enhances efficiency and data collection.
Choosing the Right Partner for Automotive Injection Molding
When considering trade for automotive injection molding, it is essential to choose a partner with extensive expertise, reliable technology, and a commitment to quality. Companies like Nolato, with significant experience in manufacturing for sectors such as electronics and medical supplies, provide the knowledge and capabilities necessary to succeed in the automotive industry.
What to Look for in a Manufacturing Partner
Key factors to consider when selecting a manufacturing partner include:
- Experience: Look for companies with a proven track record in automotive injection molding.
- Technology: Ensure they utilize state-of-the-art technology for precision and efficiency.
- Quality Control: A rigorous quality control system to deliver consistent results.
- Customer Support: Strong post-manufacturing support to address any issues or modifications.
Conclusion
In summary, the trade for automotive injection molding is not just a manufacturing process; it's a significant factor driving innovation and efficiency in the automotive industry. As manufacturers continue to explore new technologies, embrace sustainability, and focus on precision, the potential of injection molding will only grow. For businesses, partnering with experienced manufacturers like Nolato can lead to a surge in production capabilities and product quality, paving the way for success in a competitive market.