The Comprehensive Guide to Plastic Moulding Products: Innovations and Applications
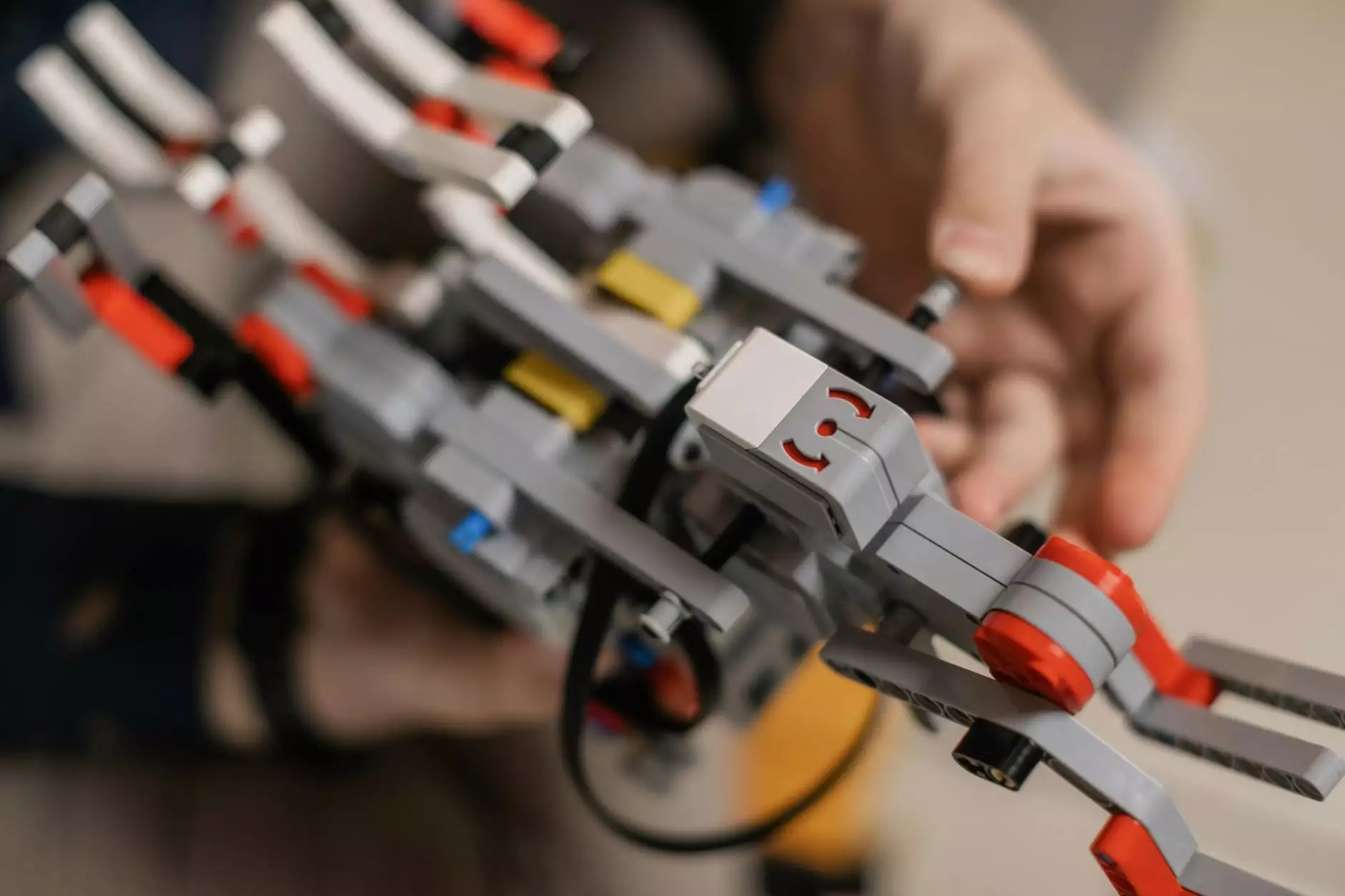
In the rapidly evolving landscape of modern industry, plastic moulding products stand out as a testament to innovation and efficiency. From the everyday objects we use to specialized components in engineering, plastic moulding is an integral part of manufacturing. This article delves deeply into the realm of plastic moulding, its significance in various sectors, and the specific processes involved. Furthermore, we’ll explore how companies like Sumiparts leverage these products within categories such as machining, laser cut, welding, plastic injection, and vulcanized industrial supplies.
Understanding Plastic Moulding Products
Plastic moulding refers to a manufacturing process that uses various techniques to create plastic products by shaping liquid or malleable plastic materials in molds. The versatility of plastics makes these products essential in numerous applications, highlighting their role in crafting complex shapes and precise specifications.
Types of Plastic Moulding Processes
Several different methods exist for producing plastic moulding products, each suited to different applications and material properties. Here are the most common types:
- Injection Moulding: One of the most popular techniques, injection moulding involves injecting melted plastic into molds. This method is highly efficient for high-volume production, yielding consistent and detailed products.
- Blow Moulding: Used primarily for hollow parts such as bottles, blow moulding forces air into a heated plastic tube, causing it to expand and conform to the mold’s shape.
- Extrusion Moulding: Continuous processes like extrusion create long shapes such as pipes and sheets by forcing melted plastic through a shaped die.
- Rotational Moulding: This technique is used for producing large, hollow plastic parts. Plastic powder is placed in a mold and rotated in an oven to evenly distribute the material along the mold's walls.
- Compression Moulding: Typically used for rubber and thermosetting plastics, this method involves placing a material in an open mold, which is then closed under heat and pressure to form the product.
Applications of Plastic Moulding Products
The applications of plastic moulding products are as diverse as the processes themselves. Here are some key industries that benefit immensely:
1. Automotive Industry
In the automotive sector, plastics are used for everything from interior components to exterior panels. Plastic moulding products are crucial for reducing weight, enhancing fuel efficiency, and improving design flexibility.
2. Consumer Goods
Everyday items that we use, such as containers, toys, and household appliances, are often produced through plastic moulding. This allows manufacturers to create engaging designs while maintaining cost-effectiveness.
3. Medical Devices
The medical field relies heavily on precise and sterile components produced through plastic moulding. Instruments, containers, and even parts of diagnostic machines utilize plastics that meet stringent safety standards.
4. Industrial Applications
From machinery parts to storage solutions in factories, plastic moulding products are integral in various industrial functionalities, offering resilience and customization.
Advantages of Plastic Moulding Products
Plastic moulding delivers numerous advantages, making it a preferred choice across industries:
Cost Efficiency
Producing large quantities of plastic components through moulding can be highly cost-effective due to reduced labor costs and minimal material wastage.
Design Flexibility
The ability to produce complex, intricate designs quickly ensures that companies can innovate rapidly and adapt to market changes.
Durability and Lightweight
Many plastics used in moulding are both durable and lightweight, making them ideal for applications where weight is a significant factor, such as in the aerospace and automotive industries.
Recyclability
Many plastic moulding products can be recycled, aligning with global efforts towards sustainability and reducing environmental impact.
Challenges in Plastic Moulding
Despite its advantages, the plastic moulding industry faces several challenges that manufacturers must navigate:
Material Selection
Choosing the appropriate plastic type for specific applications can be complicated due to the vast range of materials available, each with unique properties.
Tooling Costs
Initial tooling and mould manufacturing can be expensive and time-consuming, posing a barrier for smaller businesses looking to enter the market.
Regulatory Compliance
Adhering to regulations regarding material properties, especially in sectors like healthcare, can complicate the production process.
The Role of Sumiparts in the Plastic Moulding Market
Sumiparts specializes in a range of industrial supplies, including key services such as:
- Machining – Precision machining for customized components tailored to customer specifications.
- Laser Cut – Advanced laser cutting techniques for intricate designs and high-quality cuts.
- Welding – Robust welding solutions that ensure the structural integrity of components.
- Plastic Injection – High-quality plastic injection services that meet the demands of various industries.
- Vulcanized Industrial Supplies – Durable and reliable industrial products designed for long-lasting performance.
The expertise provided by Sumiparts allows businesses to access top-notch plastic moulding products, ensuring quality, efficiency, and reliability in their operations.
Future Trends in Plastic Moulding Products
The future of plastic moulding is promising, with trends indicating a shift towards:
1. Sustainable Practices
With environmental issues at the forefront of global discussions, the industry is moving towards more sustainable practices, including the use of biodegradable plastics and reduced waste methods in production.
2. Customization Through Technology
Advancements in technology, such as 3D printing and computer-aided design (CAD), allow for unprecedented levels of customization and innovation in plastic moulding.
3. Smart Plastics
Emerging trends include the development of 'smart' plastic materials that can change properties based on environmental factors, expanding the possibilities for product applications.
Conclusion
In conclusion, the world of plastic moulding products is vast and evolving. With companies like Sumiparts leading the way in various industrial sectors, the importance of high-quality plastic components can’t be overstated. As we progress, the blend of innovation, efficiency, and environmental responsibility will shape the future of plastic moulding, driving enhancements in design, sustainability, and adaptability across a plethora of applications.
Find Out More
For businesses and individuals interested in mastering the art of plastic moulding, or for those seeking dedicated suppliers, it is essential to explore reliable sources like Sumiparts. Discover how they can assist you in achieving your goals with robust, high-quality plastic moulding solutions.