Injection Mold Plastic: Revolutionizing Manufacturing in Metal Fabrication
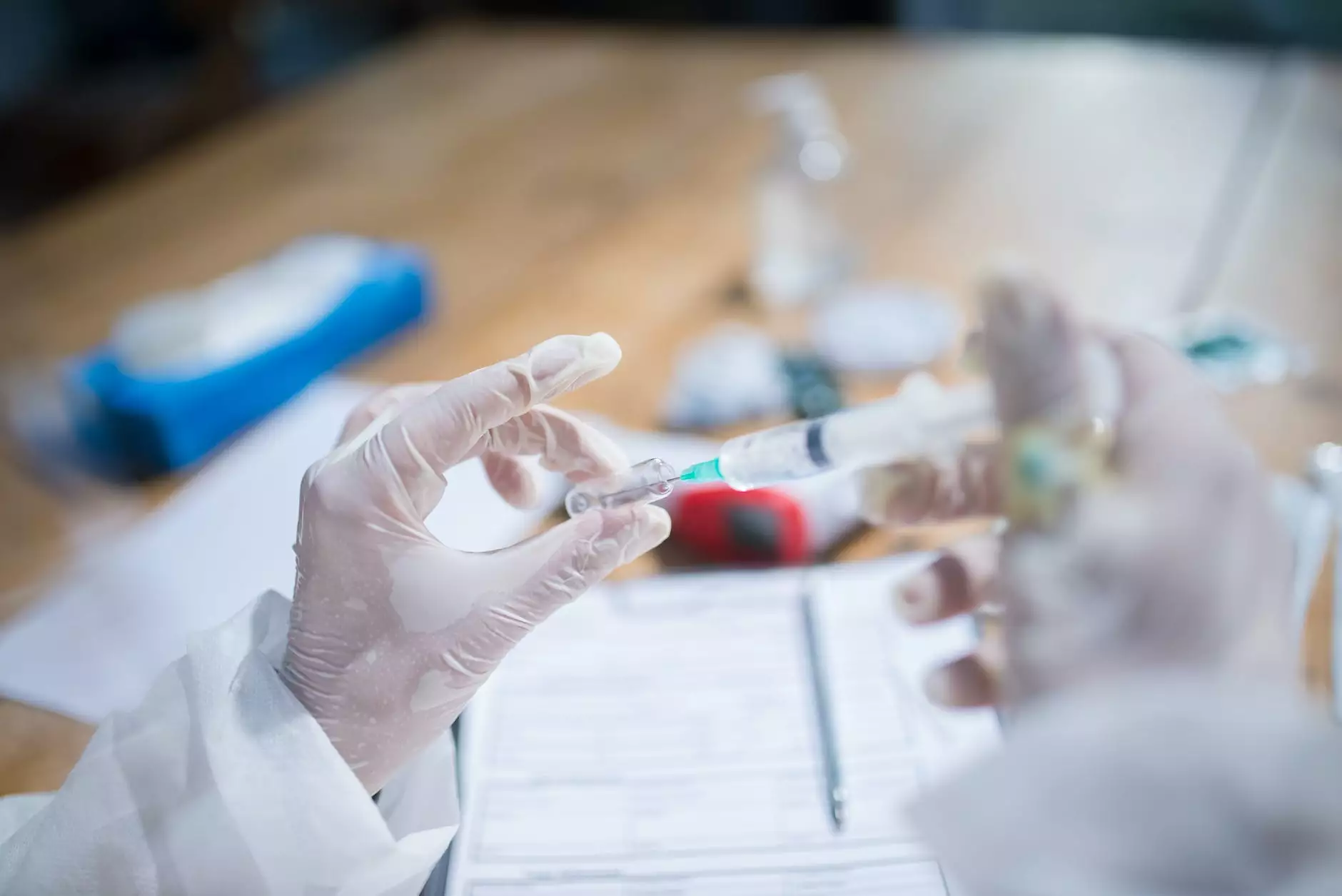
In the fast-evolving world of manufacturing, injection mold plastic has emerged as a transformative force, significantly enhancing processes in various sectors, particularly in metal fabrication. As industries strive for innovation and efficiency, understanding the advantages and applications of injection molded plastics is essential for both business leaders and professionals in the field.
The Fundamentals of Injection Mold Plastic
At its core, injection molding is a manufacturing process that involves injecting molten material into a mold to create precise parts and components. This method is widely utilized for producing plastic products but has significant implications for metal fabrication, where it can complement metal parts and aid in the production of complex assemblies.
How Injection Molding Works
The injection molding process involves several key steps:
- Material Selection: Choosing the right type of plastic is crucial. Common materials include ABS, polycarbonate, and nylon, each offering different properties suited for specific applications.
- Mold Design: Designing a mold is a critical stage, as accuracy in the design will determine the final product's quality. Molds can be intricate, allowing for detailed designs and features.
- Heating: The selected plastic is heated until it becomes molten, enabling it to flow easily into the mold.
- Injection: The molten plastic is injected into the mold under high pressure, ensuring that every detail is captured.
- Cooling: The plastic cools and solidifies in the mold, forming the desired shape.
- Demolding: Once cooled, the finished part is removed from the mold and prepared for finishing processes.
The Advantages of Injection Mold Plastic in Metal Fabrication
The integration of injection mold plastic into the metal fabrication industry offers numerous benefits:
1. Cost Efficiency
One of the most compelling advantages is cost efficiency. Unlike traditional methods, injection molding allows for mass production with minimal waste. This is particularly beneficial for businesses looking to scale operations without significantly increasing costs.
2. High Precision and Quality
Injection molded parts exhibit high levels of precision and consistency. This is essential in metal fabrication, where the parts must fit together perfectly. The accuracy of injection molding ensures that tolerances can be maintained, leading to high-quality finished products.
3. Design Flexibility
With injection molding, manufacturers can create complex shapes and designs that may not be possible with traditional metalworking techniques. This design flexibility opens up possibilities for innovation and unique product offerings.
4. Reduced Lead Times
Injection molding significantly reduces lead times for product development. Rapid prototyping allows businesses to quickly iterate designs and bring products to market faster than ever before.
5. Enhanced Material Properties
Different types of plastics can be used in the injection molding process, providing access to materials with enhanced properties such as strength, temperature resistance, and chemical stability. These attributes can complement metal components, improving overall product performance.
Applications of Injection Mold Plastic in Metal Fabrication
The applications of injection mold plastic in the context of metal fabrication are diverse and innovative. Here are some notable examples:
1. Automotive Components
In the automotive industry, the combination of metal and plastic components is prevalent. For instance, injection molded plastic parts such as dashboards, bumpers, and interior fittings are designed to work alongside metal frames and structures, reducing weight and improving fuel efficiency.
2. Electronics Enclosures
Electronics manufacturers frequently use injection molded plastic to create enclosures that house metal components. This not only protects the inner workings from physical damage but also enhances the aesthetic appeal of the product.
3. Medical Devices
The medical field benefits greatly from injection molded plastics, where reliability and safety are paramount. Components such as housings for machines, housing for tools, and disposable medical devices are often made using this method, ensuring high hygiene and precision standards.
4. Industrial Machinery
In the realm of industrial machinery, injection molded plastic is used for components that require durability and resistance to harsh conditions. Parts such as control panels, gears, and housings are crafted using this manufacturing technique, providing durability without sacrificing performance.
Environmental Considerations
As the world pivots towards sustainability, the role of injection mold plastic in reducing environmental impact cannot be overlooked. By optimizing material usage and minimizing waste, this process contributes to a greener manufacturing approach:
1. Material Efficiency
Injection molding is known for its high material efficiency. Manufacturers can create parts with minimal scrap, drastically reducing waste and lowering material costs.
2. Recyclability
Many plastics used in injection molding can be recycled, making it easier for businesses to implement sustainable practices. Reusing materials not only conserves resources but also reduces the carbon footprint of production.
3. Energy Savings
Modern injection molding machines are designed to be energy-efficient. They utilize advanced technologies that consume less energy during production, further promoting sustainability in manufacturing processes.
Choosing the Right Injection Molding Partner
Partnering with the right injection molding service can significantly influence the success of your projects. Here are critical factors to consider when selecting a partner:
1. Expertise and Experience
Look for companies that specialize in injection mold plastic and have a proven track record in the metal fabrication industry. Their experience can guide the design and production of parts that meet specific needs.
2. Technology and Equipment
The latest technology and equipment can greatly affect the quality and efficiency of production. Choose partners that invest in advanced machinery and techniques.
3. Quality Assurance
Reliable partners will have quality assurance processes in place. Ensure they adhere to stringent quality standards and perform regular audits to maintain product integrity.
4. Communication and Support
Open communication and excellent customer support are vital for successful collaboration. A partner that engages with you throughout the project will better understand and meet your needs.
The Future of Injection Mold Plastic in Metal Fabrication
The future of injection mold plastic in the metal fabrication sector looks promising. As technology continues to advance, we can expect even greater integration of plastic components in various industries. Innovations in materials science will likely produce new types of plastics with enhanced properties, allowing manufacturers to explore new horizons in design and functionality.
1. Advanced Materials
With ongoing research and development, advanced materials such as bioplastics and composites that integrate plastic and metal may become more prevalent. These materials can provide improved performance and sustainability.
2. Automation and AI
The rise of automation and AI in manufacturing will streamline the injection molding process. By incorporating smart technologies, businesses can enhance precision and efficiency, further pushing the boundaries of what is achievable in metal fabrication.
3. Sustainability Trends
As environmental awareness grows, manufacturers will increasingly focus on sustainable practices, integrating eco-friendly materials and processes into their operations to reduce their environmental impact.
Conclusion
In conclusion, the integration of injection mold plastic into metal fabrication represents an evolution in manufacturing practices. With its cost efficiency, high precision, design flexibility, and enhanced sustainability features, injection molding is set to play a pivotal role in shaping the future of the industry. By aligning with the right partners and embracing technological advances, businesses can harness the full potential of this innovative manufacturing process and stay competitive in a rapidly changing market.