The Rise of Medical Device Factories: Innovations and Practices
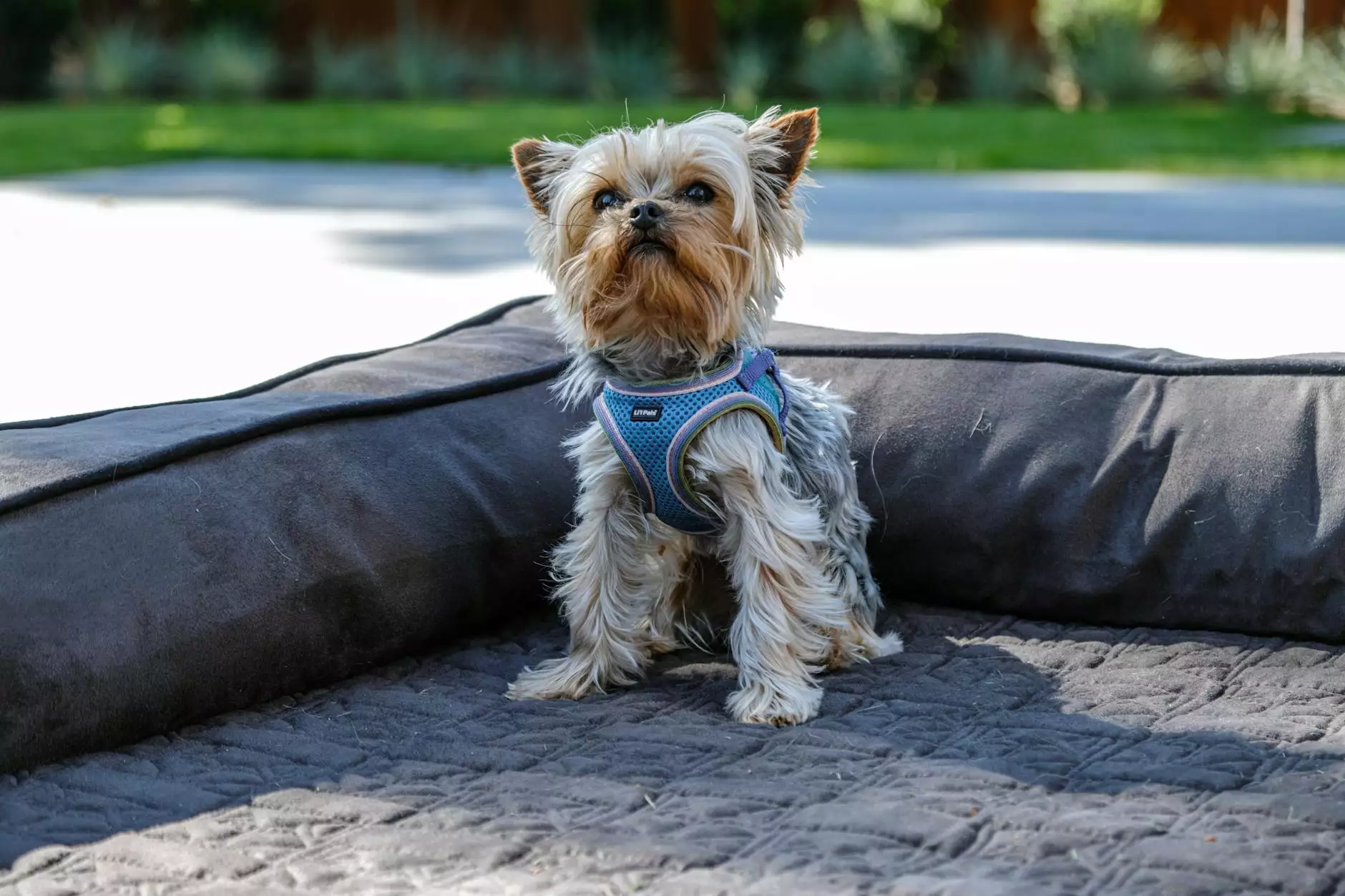
Medical device factories are at the forefront of a technological revolution, significantly impacting the healthcare industry. These factories are dedicated to the design, production, and distribution of essential medical devices that enhance patient care and improve outcomes. The growth and innovation within this sector are driven by the increasing demand for sophisticated healthcare solutions, particularly in the realm of radiation shielding materials and devices.
Understanding Medical Device Factories
At their core, medical device factories transform cutting-edge designs into tangible products that save lives. They operate under strict regulations, ensuring that every device meets safety and efficacy standards. These factories utilize modern manufacturing techniques that integrate advanced technology, automation, and quality assurance processes.
The Role of Technology in Medical Device Manufacturing
Technology plays a pivotal role in the success of medical device factories. Innovations such as 3D printing, robotics, and sophisticated quality control systems are enhancing production efficiency and accuracy. Manufacturers are investing in state-of-the-art machinery that allows for rapid prototyping and precision manufacturing, thus reducing time-to-market for new products.
Key Categories in Medical Devices
Radiation Shielding Materials
Radiation shielding materials play an essential role in protecting patients and healthcare workers from harmful radiation exposure. These materials are crucial in various medical settings, such as hospitals, clinics, and research facilities where diagnostic imaging and treatment devices are used.
Types of Radiation Shielding Materials
- Lead - Traditionally the most effective shielding material, lead is dense and provides excellent protection against gamma and X-ray radiation.
- Concrete - Used in the construction of radiation therapy suites, concrete can be an effective barrier if designed properly.
- Polymer-based Composites - These innovative materials are emerging as lighter alternatives to traditional shielding, providing flexibility and effectiveness.
- Glass - Special leaded glass is used in windows to create barriers in radiology departments while allowing visibility.
Radiation Shielding Devices
Radiation shielding devices are engineered to protect individuals from radiation exposure while allowing necessary diagnostic procedures to occur. These devices include:
- Lead Aprons - Worn by healthcare personnel during imaging procedures to shield vital organs.
- Radiation Barriers - Portable barriers that can be positioned around a patient or imaging equipment provide localized shielding.
- Shielding Shields - Fixed installations that protect areas where high levels of radiation are used.
- Custom Lead Shields - Tailored solutions designed to fit specific procedures and protect different body parts.
Quality Assurance and Regulatory Compliance
In the realm of medical device factories, maintaining strict quality assurance protocols is non-negotiable. Regulatory bodies such as the FDA in the United States or the EMA in Europe have established comprehensive guidelines that manufacturers must adhere to:
- ISO Certification - Compliance with international standards ensures that devices are produced and controlled to the highest quality levels.
- CE Marking - In Europe, medical devices must obtain CE marking, indicating conformity with health, safety, and environmental protection standards.
- Risk Management - Continuous risk assessment frameworks must be part of the lifecycle of all medical devices, particularly those involving radiation.
The Innovation Drive in Medical Device Factories
Innovation remains at the heart of medical device factories. Manufacturers are constantly seeking to enhance their product offerings through research and development. Key trends shaping this innovation include:
Smart Medical Devices
The rise of the Internet of Things (IoT) has paved the way for the development of smart medical devices. These devices can collect and transmit patient data in real time, allowing for more personalized care and better management of chronic conditions.
Biocompatible Materials
Manufacturers are increasingly exploring biocompatible materials that reduce the risk of adverse reactions in patients. The focus on developing products that seamlessly integrate with the human body is leading to new innovations in implantable devices.
Telehealth Integration
As telehealth becomes more prevalent, medical device manufacturers are designing devices that integrate seamlessly with telehealth platforms. This includes remote monitoring tools that allow healthcare professionals to track patient health metrics remotely.
Challenges Facing Medical Device Factories
Despite the many advancements, medical device factories face numerous challenges:
- Regulatory Hurdles - Navigating complex regulatory frameworks can slow down product development and approval.
- Supply Chain Disruptions - Global supply chain issues can affect the availability of critical components for medical devices.
- Competition - With the emergence of new players, established companies must continually innovate to maintain market share.
The Future of Medical Device Factories
Looking ahead, the future for medical device factories is promising, with several exciting trends on the horizon:
Sustainability Practices
There is a strong push towards sustainable manufacturing practices. Companies are exploring eco-friendly materials and processes that minimize waste and energy consumption. This shift is not only beneficial for the environment but also appealing to a growing demographic of eco-conscious consumers.
Advanced Regulatory Technologies
New technologies are emerging that streamline the regulatory compliance process. Digital solutions can ease documentation, reporting, and quality assurance procedures, reducing the burden on manufacturers.
Customized Medical Solutions
As healthcare becomes more personalized, the demand for customized medical devices will likely increase. Factories that can adapt quickly to these needs will have a competitive advantage.
Conclusion
In conclusion, medical device factories are crucial to the advancement of healthcare technology. With continuous innovations in radiation shielding materials and devices, these factories are setting new standards for patient safety and care quality. The future holds endless possibilities, as these facilities adapt to meet the evolving needs of the healthcare landscape.
For more information about cutting-edge medical device manufacturing, visit ovmdevice.com and explore our extensive range of products designed to protect and improve lives.